Authored by Altilium
Delivering critical Minerals, Made in Devon
200 years after Devon and Cornwall’s copper and tin mines helped to build the industrial world – at one point producing two thirds of the world’s copper – the South West is once again at the forefront of a new industrial revolution, thanks to an emerging EV battery supply chain that’s helping to power the UK’s transition to a cleaner, electric future.
From lithium mining in Cornwall to battery production at the UK’s largest Gigafactory in Somerset, the region is fast becoming a thriving hub for the green industries of tomorrow. And with the expansion of Altilium’s EV battery recycling operations in Plymouth, it’s also leading the way in terms of sustainability and clean tech innovation.
Founded in 2020, Altilium has spent the last five years pioneering innovative solutions to help meet the growing demands of the clean energy transition. By recycling old EV batteries and Gigafactory scrap and recovering the critical metals needed to produce new batteries, we’re ensuring these valuable resources remain in the UK – helping to make EVs even greener.
As the UK makes the transition away from fossil fuels – with the sale of new petrol and diesel cars banned from 2030 – the demand for these critical battery minerals, such as lithium and nickel, has skyrocketed. According to a recent report commissioned by the DBT, securing a supply of these minerals will be vital, not only for the transition to net zero, but for the UK’s future economic growth and security.
Currently the UK is dependent on the global market for these raw materials, with China responsible for the refining of 60-70% of lithium and cobalt found in batteries.
Developing a circular economy for these materials is critical therefore, to meet the growing demands of EV and energy storage deployment, especially in countries with limited mineral resources. As a recent study by the International Energy Agency (IEA) notes: “Battery recycling is one of the most important secondary sources of energy transition critical minerals in the future, particularly lithium, nickel and cobalt.”
Innovative green technologies
Today, Altilium is one of just a handful of companies around the world that has cracked the challenge of recycling these minerals, bringing the UK closer to a circular economy for EV batteries and reducing our dependence on international supply chains.
The recycling process begins with the dismantling and shredding of old EV batteries to produce a fine powder known as black mass. This black mass is processed using Altilium’s EcoCathode™ process, which is able to recover over 95% of the critical battery metals, including lithium. These metals are then upcycled to produce a high quality cathode active material (CAM), ready for re-use in a new battery.
By 2040, the company aims to supply 50% of the UK’s lithium and nickel from recycling, supporting industrial resilience and enabling the production of new EV batteries here in the UK.
To reach that target, Altilium is busy expanding its operations across the region, with the support of major international investors. From its humble beginnings in Tavistock, the company now employs over 50 staff across three locations, including its recently opened ACT 2 recycling facility in Plymouth, the first of its kind in the UK. The cutting-edge facility has the capacity to process the equivalent of one EV battery per day, enabling production of high volumes of battery materials for qualification with automotive customers.
Lower emissions, improved performance
As well as supporting the growth of a globally competitive battery supply chain in the UK, recycling is also helping to cut the carbon footprint of battery manufacturing. An independent lifecycle analysis (LCA) has found that cathode materials produced using Altilium’s recycled materials could be up to 74% lower in climate change impact compared to using primary mined materials from a Chinese supply chain.
Now the company is working with academic partners, such as Imperial College London, and car manufacturers, to demonstrate that recycled CAM can match the performance of commercially available materials imported from overseas. Initial analysis has already shown that Altilium’s materials can match, and even surpass, the performance of virgin mined materials, with the potential to deliver significant improvements in battery performance – including longer battery life, faster charging times and lower costs.
This March, another major milestone was achieved with the successful production of the UK’s first EV battery cells made from recycled materials, paving the way for future supply deals with automotive customers. The pouch cells were manufactured at the UK Battery Industrialisation Centre (UKBIC), the UK’s national battery manufacturing scale-up facility, using Altilium’s recycled materials and will now undergo comprehensive validation studies with a leading automotive OEM, supporting their regulatory and sustainability targets.
Future growth
The next challenge is around scaling up the business to handle the large volumes of battery waste expected in the coming decade. According to McKinsey over 100 million EV batteries are expected to reach end of life globally over the next decade. In the UK alone, the number of EV batteries reaching end-of-life is expected to reach about 1.4 million packs per year by 2040.
To process these kind of volumes, Altilium has ambitious growth plans for the coming months, including construction of a larger recycling facility in Plymouth and development of a mega-scale plant in the North East of England, creating hundreds of new green jobs for the UK.
Ultimately, the goal is to create a closed-loop supply chain, where end-of-life batteries are collected, processed and refined into battery-ready materials ready for reuse in UK gigafactories, like the one currently under construction in Somerset.
By building this circular supply chain right here in Devon, Altilium is not only keeping these valuable resources in the UK and supporting industrial resilience – it’s also ensuring that the legacy of this new green industrial revolution is a truly sustainable future for the South West.
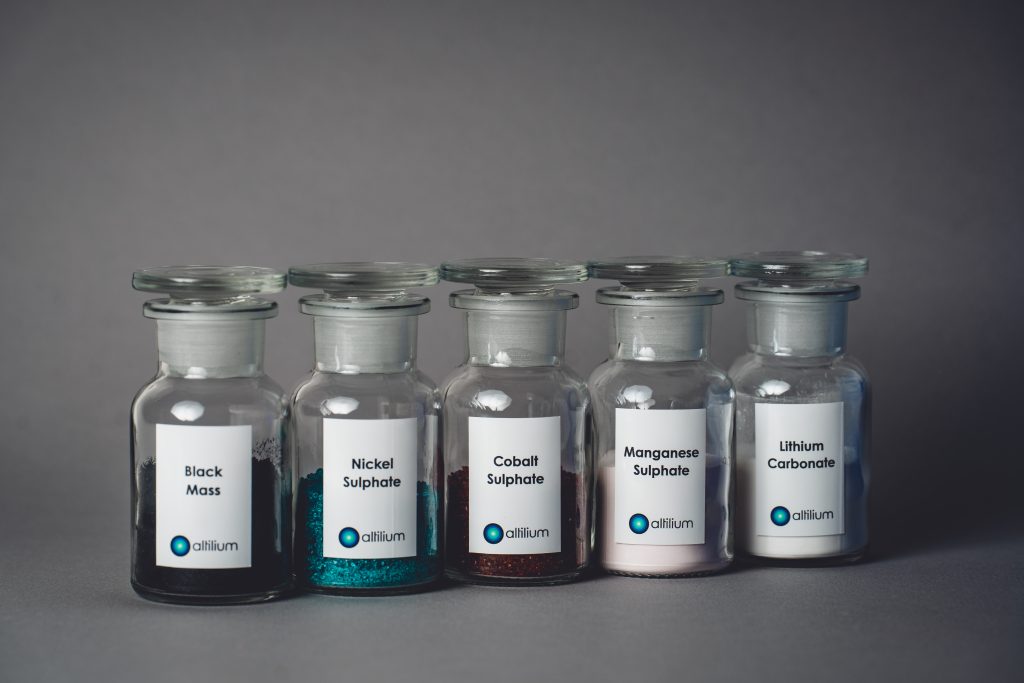